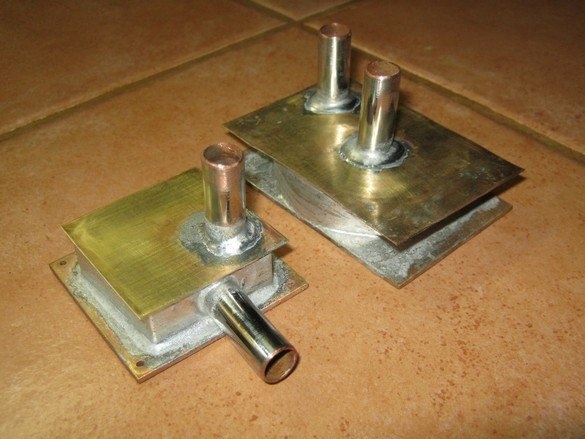
Le refroidissement par eau, malgré sa relative complexité et sa mobilité réduite, présente plusieurs avantages par rapport au soufflage d'air. Pour utilisation dans e la technologie, c'est principalement une plus grande efficacité thermique, l'absence ou radicalement moins de bruit (ventilateurs), la taille compacte des échangeurs de chaleur pour l'évacuation de la chaleur, la possibilité d'enlever facilement l'échangeur de chaleur "donnant" à l'extérieur du corps (pièce, bâtiment) de l'appareil.
Le refroidissement à l'eau peut être appliqué dans certains cas dans des dispositifs fixes ayant des pièces qui génèrent de la chaleur de manière intensive et nécessitent un refroidissement. En technologie électronique, il peut s'agir d'étages de sortie d'émetteurs, d'amplificateurs puissants (SP) fonctionnant en classe A, d'électronique de puissance. Une tâche courante est l'utilisation du refroidissement par eau pour l'unité centrale d'un ordinateur personnel. Ce dernier permet de réduire considérablement le bruit des ventilateurs de l'instrument, la pénétration de la poussière dans le boîtier de l'instrument et d'augmenter l'efficacité de refroidissement.
En vente, il existe des ensembles de constructeurs prêts à l'emploi qui permettent de remplacer les ventilateurs réguliers de l'unité centrale par des bidons, des tuyaux, des pompes et les composants de ces systèmes séparément. Ici, la technologie de fabrication simple et pratique de l'élément peut-être le plus cher et le plus complexe - un échangeur de chaleur - pour l'évacuation de la chaleur est donnée. La technologie permet la maison conditions, sans accès aux machines, font un échangeur de chaleur plat miniature efficace. La préparation de la soudure et la soudure elle-même sont très simples. Un ajustement fin de petites pièces n'est pas nécessaire. La configuration de l'échangeur de chaleur peut être facilement adaptée à la tâche en cours. Les exigences en matière de matériaux sont également facilitées - aucun lingot massif d'alliage de cuivre n'est requis; une plaque d'une épaisseur de plusieurs millimètres suffit.
Ce qui était nécessaire pour travailler.
Des outils
Un ensemble d'outils d'établi, des ciseaux métalliques, une scie à métaux. Une scie sauteuse à bijoux avec accessoires est bien pratique, mais vous pouvez vous en tirer. Outil de marquage, petit étau. Un petit brûleur à gaz a été utilisé pour le soudage.
Matériaux
Billettes de fer - feuille de cuivre, laiton. Tubes de diamètre approprié. Papier de verre, soudure, flux pour le brasage.
Voici la fabrication d'un ensemble d'échangeurs de chaleur pour l'unité centrale d'un ordinateur personnel (processeur, carte vidéo). Les dimensions des échangeurs de chaleur ont été dictées par les fixations des radiateurs standard avec soufflage - les supports de trophées ont été utilisés au maximum dans la nouvelle conception. La configuration des buses a été déterminée par la commodité de la connexion avec des tuyaux. En fonction du diamètre des tuyaux de raccordement au niveau de la pompe de circulation, le diamètre des tuyaux est de 10 mm.
Comme base de l'échangeur de chaleur - les semelles adjacentes à la puce, une plaque en laiton de 2,5 mm d'épaisseur a été utilisée. Après le marquage, deux billettes rectangulaires ont été découpées à l'aide d'une scie à métaux. Les extrémités des pièces sont alignées avec une lime, les arêtes vives sont ternes. Par plusieurs nombres de petites peaux, les plans de la pièce sont traités. Le côté avec un minimum de rayures est attribué à l'extérieur - au CHIP; il est préférable de le marquer avec un stylo-feutre à alcool.
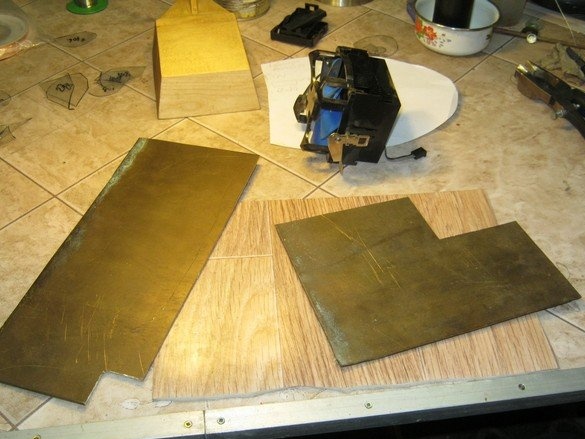
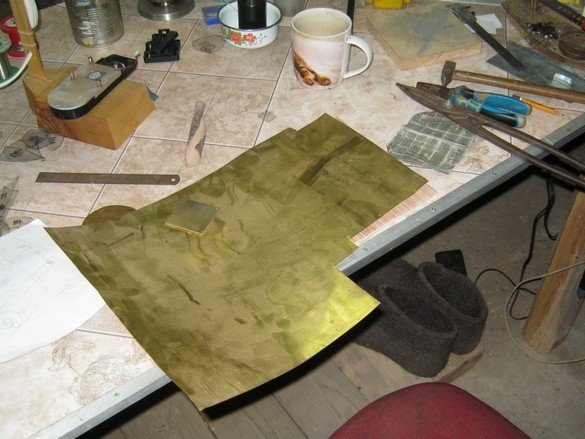
Toutes les autres parties des échangeurs de chaleur sont tout à fait acceptables pour fonctionner à partir d'un métal beaucoup plus mince - presque une feuille. Avec un montage volumétrique rigide par soudure, la conception est très solide et fiable. Ici, une feuille de laiton de 0,2 mm d'épaisseur est appliquée. En fonction du diamètre des tuyaux et tuyaux de raccordement, la hauteur de l'échangeur de chaleur a adopté 10 mm Dans l'échangeur de chaleur du processeur, la hauteur de 11 à 12 mm était due au montage utilisé. Dans l'échangeur de chaleur CHIP de la carte vidéo, le tuyau d'entrée était commodément réalisé dans une extrémité plate. Le trou dans la bande était marqué avec une boussole-ballerine et scié avec un fichier de scie sauteuse n ° 6. Les trous restants pour les buses des capuchons plats sont réalisés de la même manière.
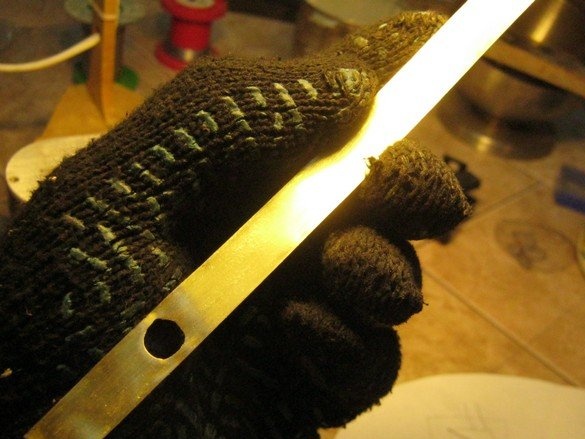
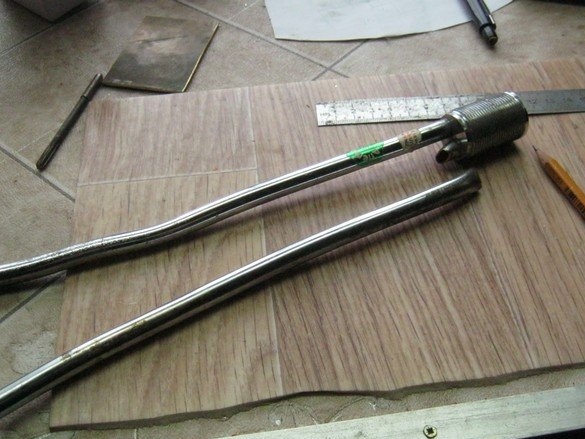
Les tuyaux eux-mêmes sont constitués de morceaux d'un tube en cuivre-chrome provenant d'une ancienne plomberie.
Après un décapage approfondi (pour le brasage), la bande de laiton pour les parois latérales basses est pliée avec une sorte d'escargot sur le tube-blank du tuyau. Ensuite, un escargot de l'échangeur de chaleur en est formé, de sorte qu'au début et à la fin de celui-ci, il y a suffisamment d'espace pour que les tuyaux et les parois ne se ferment pas trop hermétiquement et ne dépassent pas des bords de la semelle. Par le nombre de tours, il est possible dans une certaine mesure de réguler la quantité de chaleur transférée au liquide de refroidissement (eau). En général, nous fonctionnons de manière intuitive - plus la zone nécessitant un refroidissement est grande et plus elle est chauffée, plus il faut de tours.
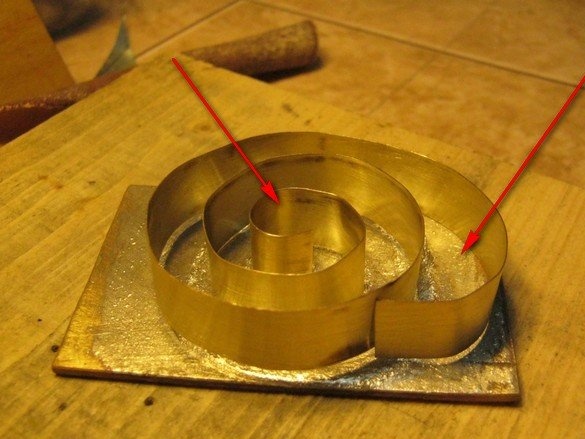
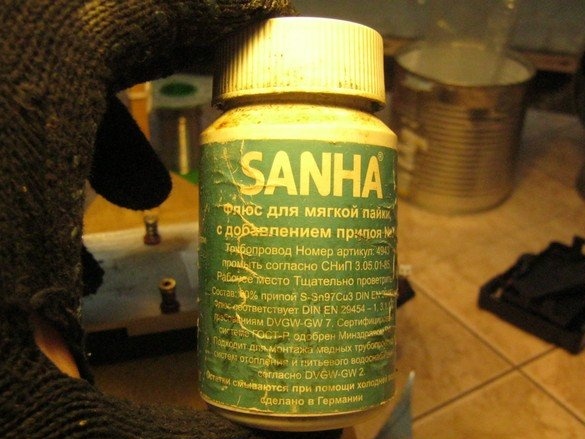
Lors du soudage, un flux de «plomberie» a été utilisé pour souder un tuyau en cuivre avec un brûleur. Il est conçu pour une soudure étain-cuivre sans plomb, mais il fonctionne parfaitement avec du plomb étain ordinaire, ce qui est très pratique - ce dernier est moitié moins cher. Vous pouvez probablement utiliser des flux inorganiques liquides, le même «acide de soudure» (chlorure de zinc). La colophane et les flux fondés sur celle-ci ne doivent pas être utilisés pour le soudage à flamme nue - ils s'enflamment facilement, même s'ils sont chauffés par l'arrière, après la combustion, ils laissent de la suie rendant le soudage difficile.
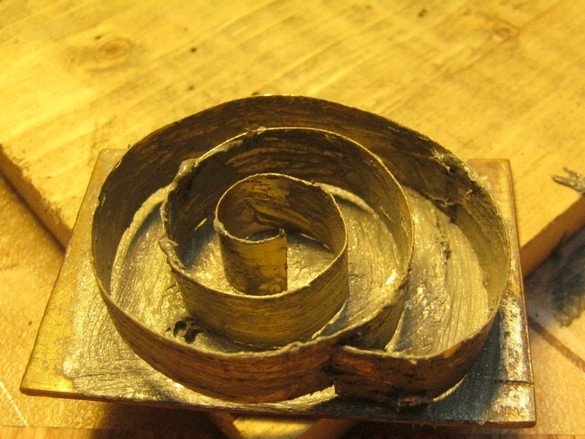
Après avoir appliqué le flux, le ruban enroulé doit être fermement pressé sur la base. Pour ce faire, vous avez besoin d'une plaque technologique et d'une paire de pinces à linge métalliques ou d'un poids. À l'intérieur du contour, placez uniformément de petits morceaux de soudure. Ici, nous avons utilisé le POS-60 sous la forme d'un fil de 2,5 mm d'épaisseur. Il l'a coupé avec des couteaux en particules de 5 ... 7 mm.
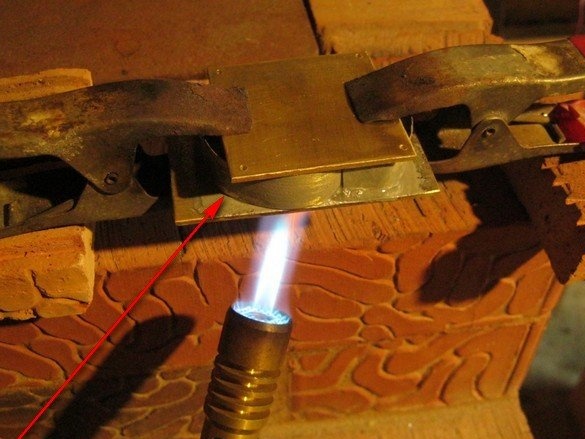
Nous chauffons jusqu'à ce que la soudure fonde et resserre complètement le contour de notre clôture d'escargot. Entre la semelle et le mur. Il faut se rappeler que la soudure coule dans un endroit avec une température plus élevée. Si la soudure n'est pas tirée dans une certaine zone, vous pouvez l'aider en la touchant ou en la caressant avec une brindille de soudure «externe». Vous ne devez pas chauffer la pièce pendant très longtemps - le flux est brûlé et cesse de fonctionner.Dans ce cas, il est nécessaire de refroidir la pièce, de démonter, de nettoyer et de tout recommencer. Mais avec un nettoyage soigneux des surfaces et beaucoup de flux, tout fonctionne très bien.
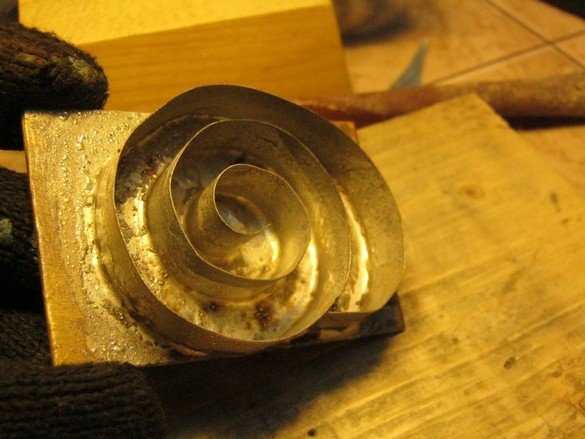
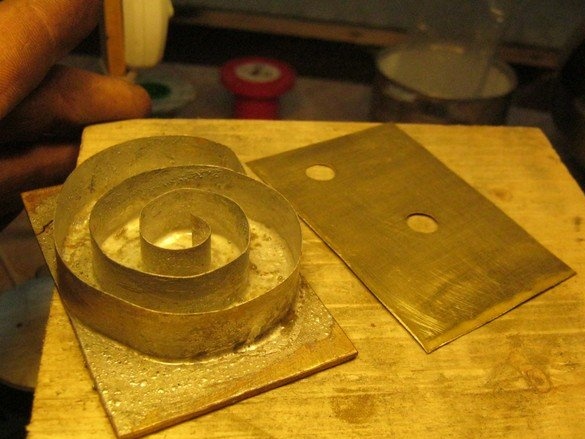
J'ai coupé un couvercle dans la même feuille de laiton épaisse, marqué et découpé deux trous pour les buses avec une scie sauteuse à bijoux. La forme du couvercle est rectangulaire en forme de semelle. Il s'avère plus esthétique et plus pratique. Si le matériau n'est pas particulièrement cher (feuille épaisse), je recommande cette forme. Soit dit en passant, ma feuille de 0,2 mm est coupée avec succès avec de grands ciseaux de tailleur grossiers, bien que ceux spéciaux pour le métal soient certainement plus pratiques.
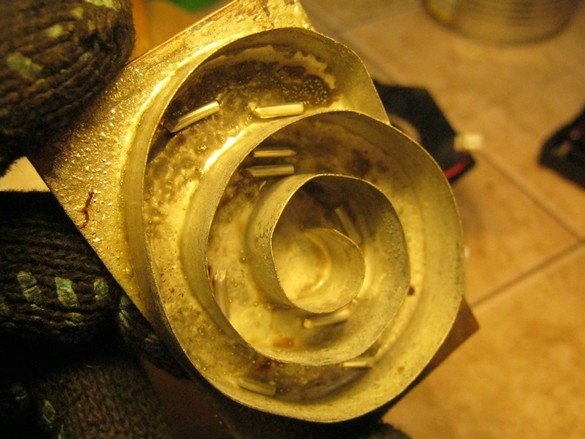
Après avoir fabriqué le flan du capot supérieur, nettoyez-le soigneusement et appliquez le flux. Sur le couvercle et les bords supérieurs de la cochlée. À l'intérieur, nous déposons à nouveau les morceaux de soudure, assemblons le tout et fermons le couvercle. Au cas où, vous pouvez secouer le flan de l'échangeur de chaleur de sorte que les morceaux de soudure, probablement collés aux murs ou au plafond (flux - pâte épaisse) tombent au fond (couvercle). Encore une fois, nous chauffons le brûleur, si nécessaire, nous brandissons une tige de soudure à l'extérieur. Laissez refroidir.

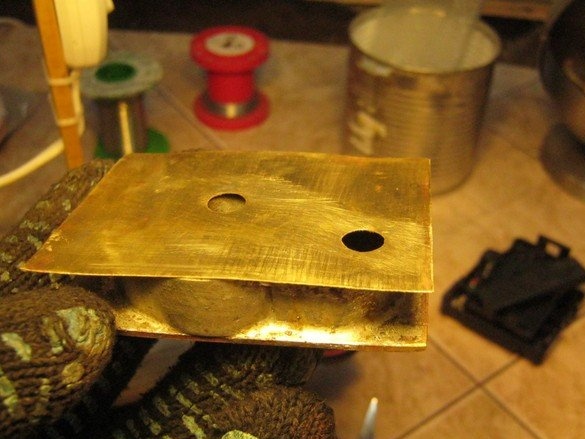
Le couvercle de l'échangeur de chaleur a été soigneusement nettoyé avec un papier de verre fin et préparé une paire de raccords de tuyau. Étant donné que mes pièces sont en plomberie chromée, il est préférable de dénuder les bords pour les souder au cuivre. La soudure sur le revêtement n'est pas pire, mais la résistance d'une telle connexion sera moindre - les revêtements anciens ont également tendance à se décoller.
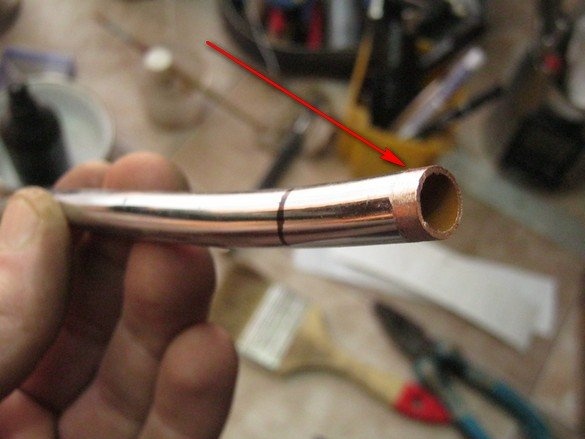
Je l'ai scié avec une scie à métaux pour le métal, l'ai nettoyé, mis un flux dessus et enveloppé un anneau de soudure sur chaque raccord.
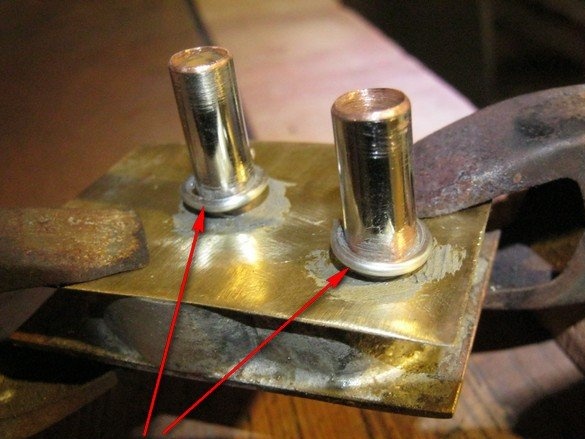
Avec un chauffage soigneux avec une petite flamme du brûleur, afin que le reste ne se dissolve pas, la soudure fond, glisse avec un rouleau soigné. Il est préférable de chauffer le raccord lui-même, et après avoir fondu la soudure, un peu et un couvercle autour de lui.
Une fois l'échangeur de chaleur complètement refroidi, tout ce qui est disponible doit être soigneusement lavé du flux avec de l'eau chaude et une brosse dure. Le flux à l'intérieur devra être lavé - après avoir assemblé le système de refroidissement fermé, vous devez changer l'eau 3-4 fois, disons tous les 2 jours de fonctionnement. C'est exactement ce que le fabricant de flux conseille dans le cas de l'installation d'une alimentation en eau en cuivre.
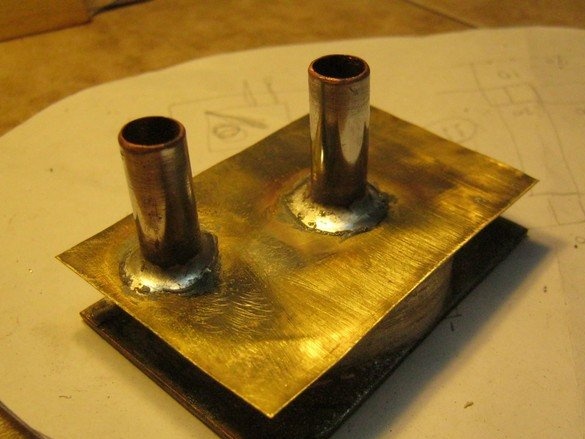
L'échangeur de chaleur pour la puce de la carte vidéo est plus petit, la configuration simplifiée de la cochlée interne et l'emplacement des raccords. Une autre méthode de fixation consiste à utiliser quatre vis à ressort standard. En général, la technologie est complètement similaire.
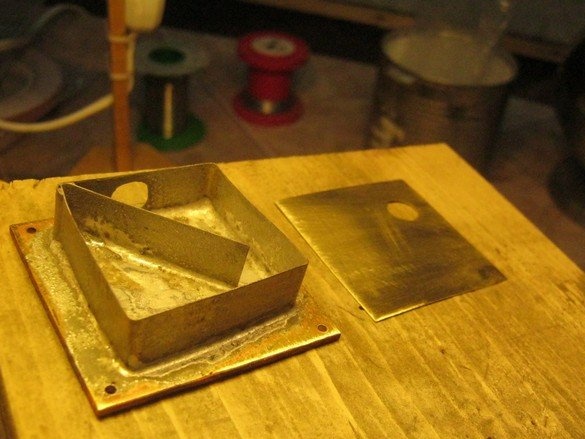
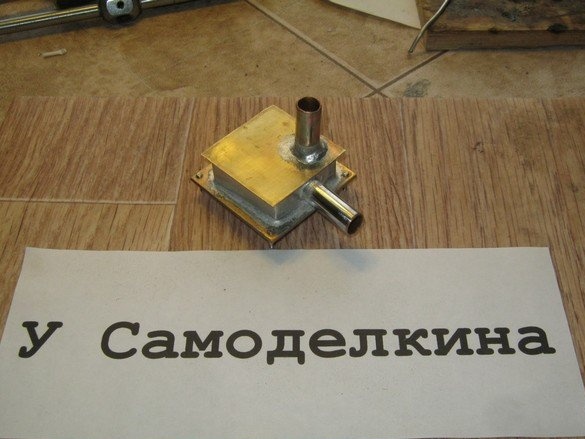
Conclusions
La pratique a montré la fiabilité, la disponibilité et une efficacité de conception suffisante. Avec la simplicité de fabrication, la technologie semble tout à fait raisonnable et recommandée pour la répétition.
Il faut dire quelques mots sur la sélection des matériaux. Puisqu'une bonne conductivité thermique (semelles) est requise, il est préférable d'utiliser du cuivre ou des alliages de cuivre, entre autres, cela simplifiera le choix des flux pour le brasage. Il doit également, bien entendu, être exclu de la conception des métaux formant une paire galvanique avec le cuivre.
Babay Mazay, janvier 2019