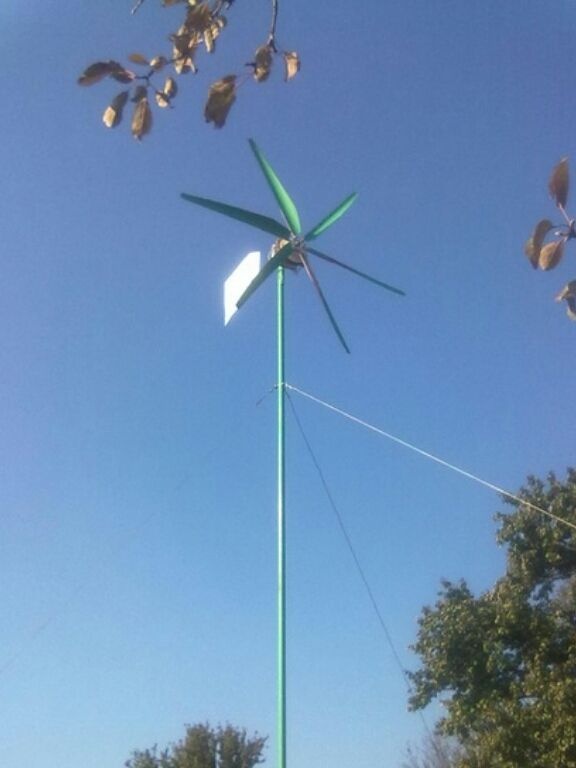
Cet article est consacré à la création d'un générateur d'aimant axial en néodyme avec stators sans métal. Les moulins à vent de cette conception sont devenus particulièrement populaires en raison de la disponibilité croissante des aimants en néodyme.
Matériaux et outils utilisés pour construire le moulin à vent de ce modèle:
1) le moyeu de la voiture avec disques de frein.
2) une perceuse avec une brosse métallique.
3) 20 aimants en néodyme mesurant 25 sur 8 mm.
4) résine époxy
5) mastic
6) tuyau en PVC de 160 mm de diamètre
7) treuil à main
8) tuyau métallique de 6 mètres de long
Considérez les principales étapes de la construction d'un moulin à vent.
Le moyeu de la voiture avec un disque de frein a été pris comme base du générateur. Étant donné que l'essentiel de la production en usine, cela servira de garant de la qualité et de la fiabilité. Le moyeu a été complètement démonté, les roulements à l'intérieur ont été vérifiés pour leur intégrité et lubrifiés. Depuis que le moyeu a été retiré de l'ancienne voiture, la rouille a dû être nettoyée avec une brosse, que l'auteur a plantée sur la perceuse.
Ci-dessous, une photographie du hub.
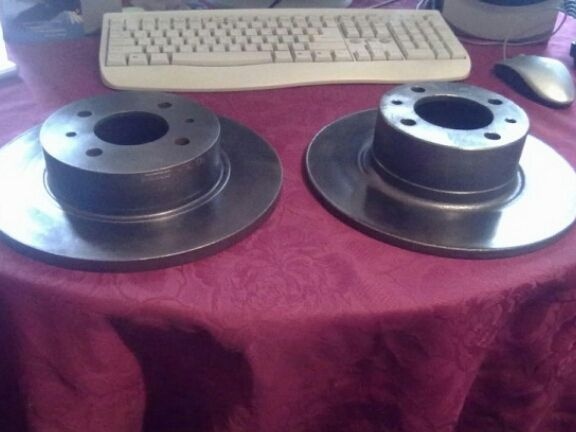
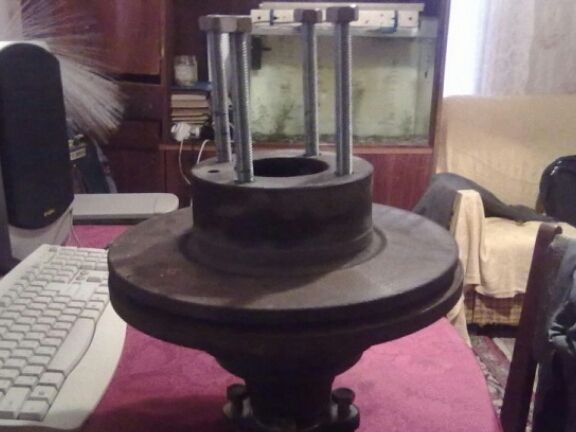
L'auteur a ensuite installé des aimants sur les disques du rotor. 20 aimants ont été utilisés. De plus, il est important de noter que pour un générateur monophasé le nombre d'aimants impliqués est égal au nombre de pôles; pour un générateur biphasé, le rapport sera de trois à deux ou de quatre pôles à trois bobines. Les aimants doivent être montés sur des pôles alternés. Pour maintenir la précision, vous devez créer un modèle de mise en page sur papier ou dessiner des lignes de secteurs directement sur le disque lui-même.
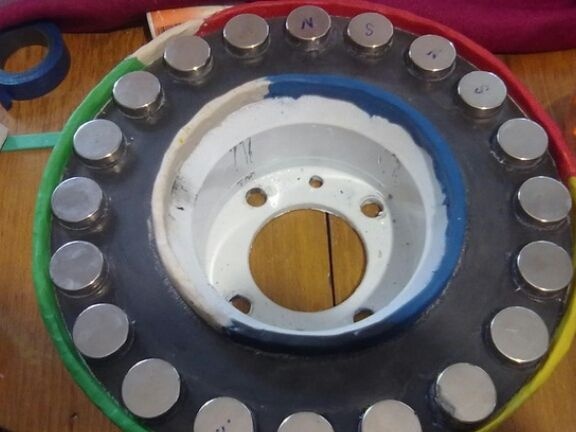
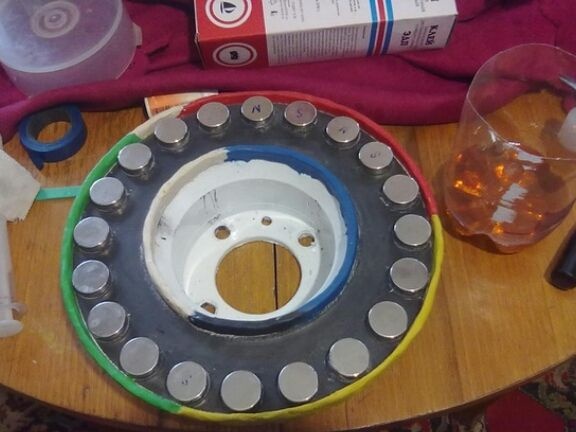
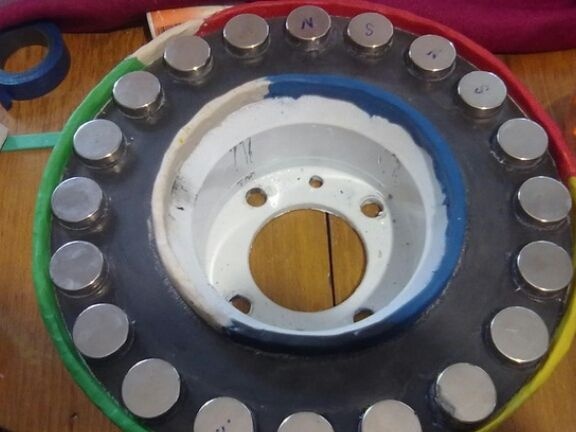
Vous devez également marquer les aimants aux pôles avec un marqueur. Vous pouvez déterminer les pôles en déplaçant les aimants tour à tour d'un côté de l'aimant de contrôle, s'ils sont attirés - plus, repoussés - moins, l'essentiel est que les pôles alternent lorsqu'ils sont installés sur un disque. Cela est nécessaire car les aimants des disques doivent être attirés les uns vers les autres, et cela ne se produira que si les aimants opposés seront de polarité différente.
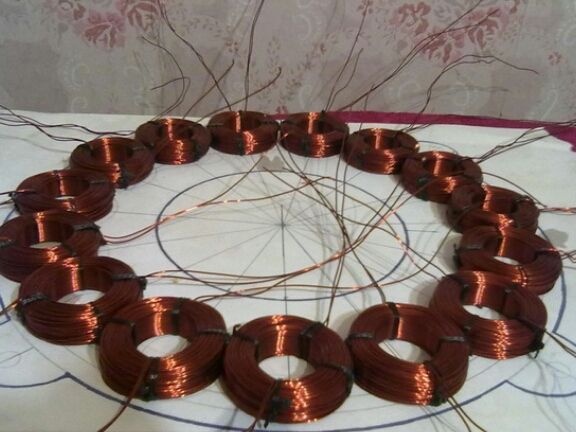
Les aimants ont été collés aux disques avec de l'époxy. Pour empêcher la résine de se propager au-delà des limites du disque, l'auteur a fait des bordures le long des bords avec du mastic, la même chose peut être faite avec du ruban adhésif, simplement en enroulant la roue en cercle.
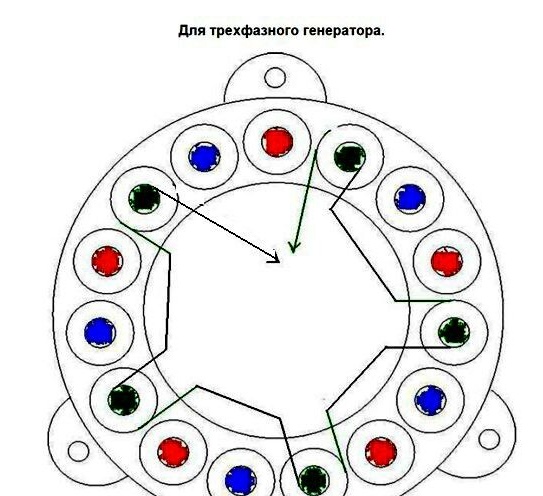
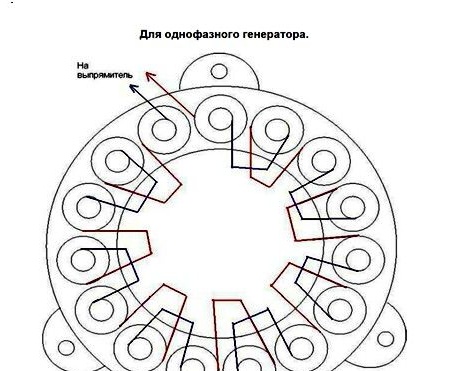
Considérez les principales différences dans la conception des générateurs monophasés et triphasés.
Un générateur monophasé produira des vibrations sous des charges, ce qui affectera la puissance du générateur lui-même.La conception triphasée est dépourvue d'un tel inconvénient en raison de quoi, la puissance est constante à tout moment. En effet, les phases compensent la perte de courant les unes dans les autres. Selon les estimations prudentes de l’auteur, la conception triphasée dépasse de 50% la conception monophasée. De plus, en raison du manque de vibrations, le mât ne se balancera pas en plus, il n'y aura donc pas de bruit supplémentaire pendant le fonctionnement du rotor.
Lors du calcul de la charge de la 12e batterie, qui commencera à 100-150 tr / min, l'auteur a effectué 1000 à 1200 tours en bobines. Lors du bobinage des bobines, l'auteur a utilisé l'épaisseur maximale autorisée du fil pour éviter la résistance.
Pour enrouler le fil autour des bobines, l'auteur a construit une machine artisanale dont les photos sont présentées ci-dessous.

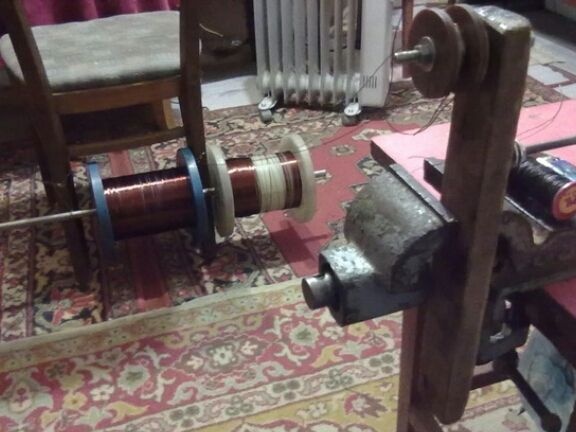
Il est préférable d'utiliser des bobines de forme ellipsoïdale, ce qui permettra à une densité plus élevée de champs magnétiques de les traverser. Le trou intérieur de la bobine doit être fait en fonction du diamètre de l'aimant ou plus. Si vous les réduisez, les parties frontales ne participent pratiquement pas à la production d'électricité, mais servent de conducteurs.
L'épaisseur du stator lui-même doit être égale à l'épaisseur des aimants impliqués dans l'installation.
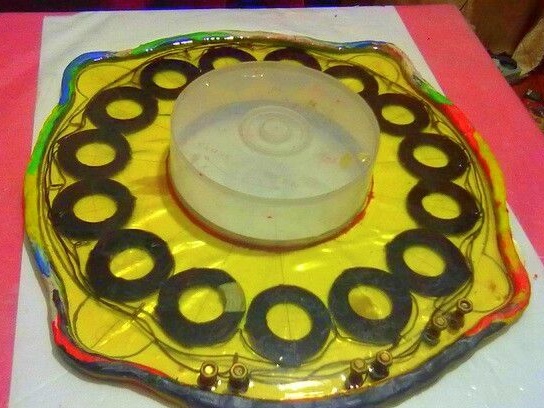

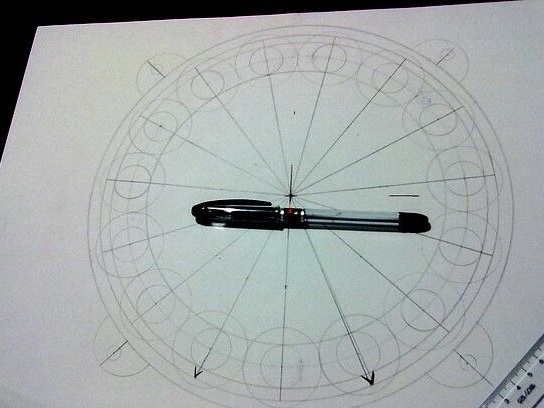
La forme du stator peut être en contreplaqué, bien que l'auteur ait décidé cette question différemment. Un modèle a été dessiné sur papier, puis les côtés ont été réalisés avec du mastic. De plus, la fibre de verre était utilisée pour la résistance. Afin d'éviter que l'époxy ne colle au moule, il doit être lubrifié avec de la cire ou de la vaseline, ou vous pouvez utiliser du ruban adhésif, un film qui peut ensuite être arraché de la forme finie.
Avant de couler les bobines, il est nécessaire de les fixer avec précision, ainsi que leurs extrémités hors du moule, de manière à ensuite connecter les fils avec une étoile ou un triangle.
Après que la partie principale du générateur a été assemblée, l'auteur a mesuré testé son travail. Avec une rotation manuelle, le générateur génère une tension de 40 volts et une intensité de courant de 10 ampères.
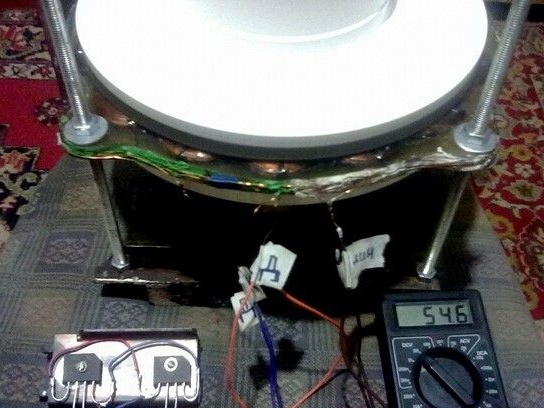
Puis l'auteur a fait un mât pour un générateur de 6 mètres de haut. À l'avenir, il est prévu d'augmenter la hauteur du mât en utilisant un tuyau plus épais au moins deux fois. Que le mât était immobile, la base était inondée de béton. Un support métallique a été conçu pour abaisser et soulever le mât. Cela est nécessaire pour avoir accès à la vis au sol, car il n'est pas particulièrement pratique d'effectuer des travaux de réparation en hauteur.
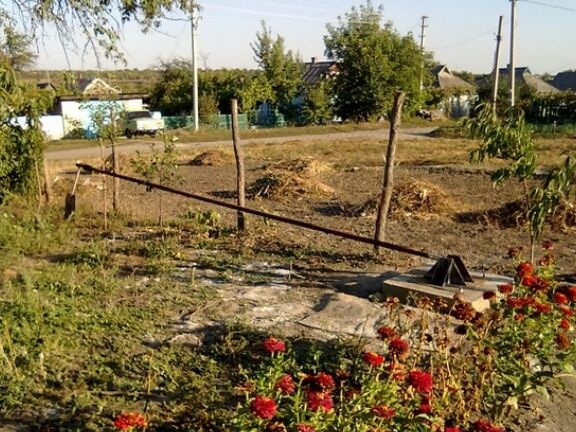
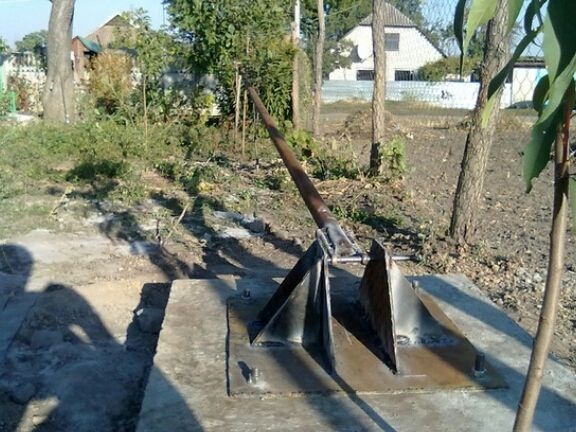
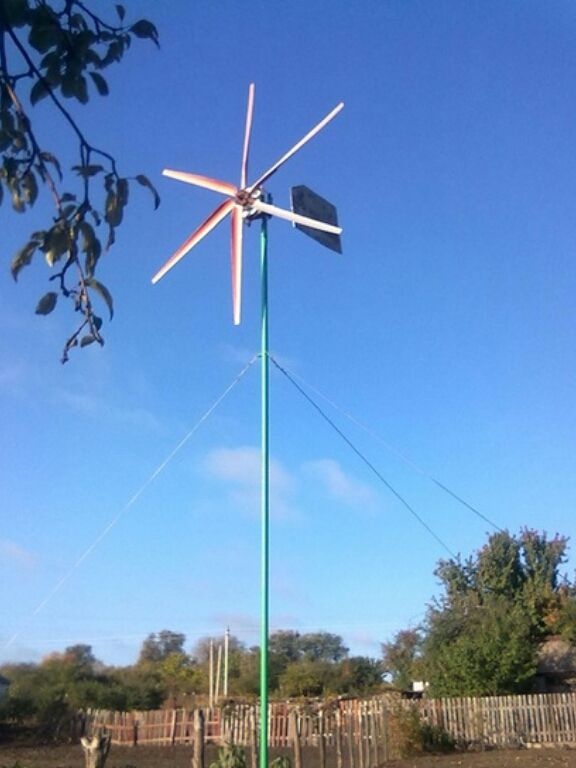
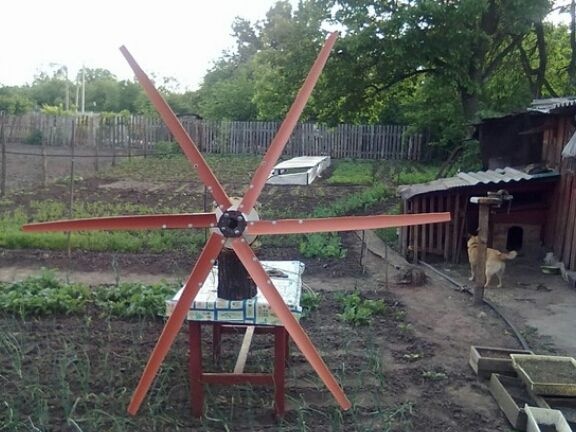
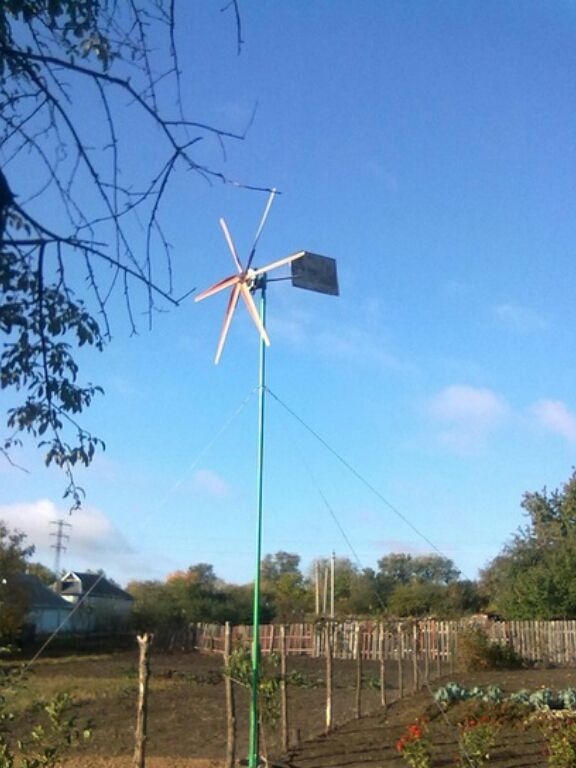
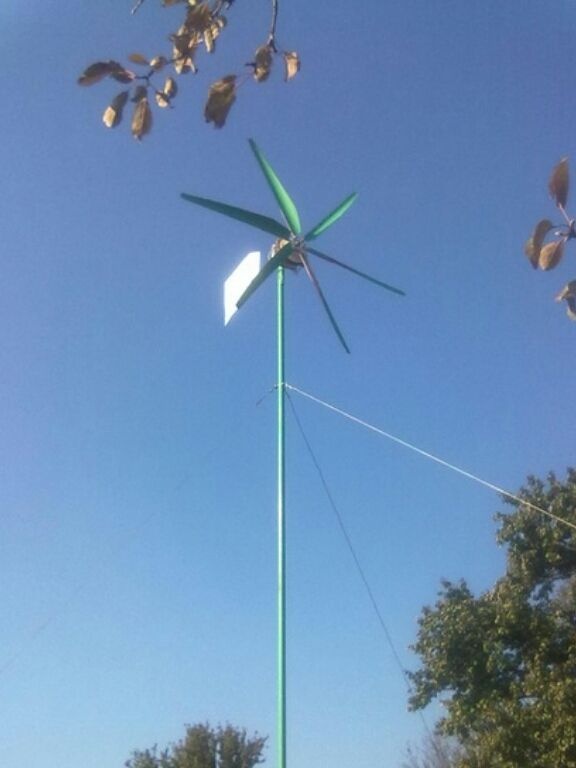
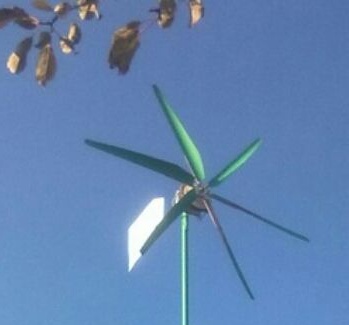
Un treuil manuel est utilisé pour soulever le mât.
La vis du générateur lui-même était en tube PVC d'un diamètre de 160 mm.
Après avoir installé et testé le générateur dans des conditions standard, l'auteur a fait les observations suivantes: la puissance du générateur atteint 300 watts avec un vent de 8 mètres par seconde. Par la suite, il a augmenté la puissance du générateur en raison des noyaux métalliques installés dans les bobines. La vis commence à deux mètres par seconde.
De plus, l'auteur a commencé à améliorer la conception afin d'augmenter la puissance du générateur. Des noyaux magnétiques de plaques ont été dessinés, qui ont ensuite été installés dans la structure. Du fait de leur installation, un effet collant est apparu, mais pas très fort. La vis démarre à une vitesse du vent d'environ deux mètres par seconde.
Ainsi, l'installation de noyaux métalliques a augmenté la puissance du générateur à 500 watts avec un vent de 8 mètres par seconde.
Pour se protéger contre les vents forts, un circuit d'hélice de queue repliable classique a été utilisé.
En moyenne, un générateur est capable de générer jusqu'à 150 watts d'énergie par heure, ce qui est utilisé pour charger les batteries.