En regardant à travers les graveurs laser sur aliexpress, le maître est tombé sur plusieurs modèles alimentés par USB. C'était incroyable qu'ils puissent graver sur différents matériaux, ainsi que découper des formes et des motifs à partir d'autocollants et de papier, et faire toute cette puissance à partir de l'USB 5V. Mais l'inconvénient de ces graveurs était qu'ils avaient une petite zone de travail, dans la plupart des cas seulement 40 mm x 40 mm.
Ensuite, le maître a décidé de concevoir et de fabriquer indépendamment un graveur à l'aide d'une imprimante 3D pour la fabrication. En cours de route, il a décidé de rendre le support laser modulaire afin que le laser puisse être facilement remplacé par un stylo ou un marqueur. Une fonction de connexion Bluetooth a également été ajoutée.
Les spécifications du graveur sont les suivantes:
- Zone de travail 200 x 162 mm
-1000 mw module laser
-Fonctionne à partir d'une source d'alimentation USB (5V)
-Fonction de guidage automatique
- Communication Bluetooth entre graveur laser et PC
- Contrôle laser PWM. (Aide à créer différentes nuances de noir lors de la gravure de portraits)
-102,4 pas par résolution mm
- La machine peut graver, couper et dessiner sur différents matériaux
Outils et matériaux:
-Arduino UNO;
-Carte d'extension;
- Pilote de moteur pas à pas A4988 - 2 pièces;
-1 000 mW module laser;
- Arduino Nano;
- Convertisseur Boost XL6009;
- Roulements à billes linéaires LM8UU - 6 pièces;
Poulie - 4 pièces;
- Tiges diamètre 8 mm, longueur 300 mm -4 pcs;
-Module IRF520 Mosfet;
- Relais;
- Interrupteurs de fin de course - 2 pièces;
-Moteurs pas à pas 2 pcs;
- Aimants néodyme 18 x 5 mm x 3 mm;
-30 * 30 mm ventilateur de refroidissement 5 volts;
-Ceinture;
-HC-05 module Bluetooth;
-Servomoteur SG90;
Bornes à vis
-Rétrécir le tube;
- Superglue;
-Cravates de câble;
-Fixations
M3 30mm
Boulons M3 12 mm
M4 40mm
Écrous M3
Écrous M4;
- Contreplaqué 8 mm 48 x 42 cm;
- Feuille acrylique transparente de 5 mm 22 x 22 cm;
- Câble MicroUSB;
-Papier déchet;
-Nadfil;
- tournevis;
-Accessoires de soudure;
- Pinces;
- ciseaux;
-Pinces;
-Ordinateur avec logiciel;
Première étape: conception
L'assistant a commencé par concevoir la base et les supports de l'arbre de l'axe Y. Comme les supports sont constitués de deux composants identiques, la fonction de miroir du Fusion 360 a facilité le travail. La fonction miroir a été utilisée plusieurs fois dans le développement de ce graveur laser.Contrairement aux autres logiciels de CAO, l'une des grandes fonctionnalités de Fusion 360 est qu'il vous permet de créer plusieurs composants sur un seul écran avec un lien vers d'autres composants, c'est-à-dire le modèle peut être conçu assemblé.
La hauteur des guides de l'axe X dépend de la distance focale du laser utilisé. Il vous suffit de vous assurer que la hauteur du laser se situe dans cette plage. La mise au point finale du faisceau laser peut être effectuée en ajustant la lentille sur le laser.
Fusion 360 vous permet également de choisir l'apparence et le matériau des composants pour donner une apparence réelle à la conception finale. Le programme vous permet de convertir et d'enregistrer les composants développés directement au format STL pour l'impression 3D.
Ci-dessous, vous pouvez télécharger le fichier Fusion 360 avec le projet de graveur.
graveur laser v16.f3d
Deuxième étape: impression 3D
Ensuite, l'assistant commence à imprimer les détails. Toutes les pièces sont conçues de manière à pouvoir être facilement imprimées dans une imprimante 3D sans supports.
L'assistant imprime les détails sur une imprimante 3D TEVO.
Matériel: PLA (vert foncé)
Hauteur de couche: 0,3 mm
Remplissage: 30%
Épaisseur de paroi: 0,8 mm
Épaisseur haut / bas: 0,9 mm
Les fichiers à imprimer peuvent être téléchargés en cliquant sur ce le lien.
Troisième étape: assemblage de l'axe Y
L'assistant vous conseille d'ouvrir le fichier de construction du PC Fusion 360 avant l'assemblage. Cela aide à rendre le processus de construction plus compréhensible.
L'assistant installe les tiges et les roulements linéaires. Le maître conçu pour éviter de coller des pièces, c'est-à-dire l'ajustement est serré. Les tiges doivent être remplies dans le siège avec un marteau.
Après l'assemblage, assurez-vous que le chariot se déplace librement.
Quatrième étape: bureau
Un trou est percé sur une feuille acrylique. Visse la feuille sur le chariot et définit les bords de la feuille exactement parallèlement aux bords du chariot. Marque et perce quatre trous de montage. Vis acrylique sur le chariot.
Cinquième étape: axe X
Ensuite, le maître récupère l'axe X. Les guides de l'axe ont été imprimés par le maître, car ceux qu'il a achetés se sont avérés défectueux. Selon lui, après le meulage et la lubrification, ces guides ne fonctionnent pas moins bien que ceux achetés.
Étape six: retravailler le moteur unipolaire 28BYJ-48 en bipolaire
Il y a deux raisons principales pour lesquelles vous devez convertir un moteur unipolaire en moteur bipolaire.
L'algorithme de commande de moteur bipolaire utilisant le pilote de moteur pas à pas A4988 est plus simple que de contrôler un moteur unipolaire
La carte d'extension prend uniquement en charge les moteurs pas à pas bipolaires.
Vous pouvez refaire le moteur en trois étapes.
Ouvrez le boîtier en plastique bleu, déconnectez le fil rouge de la carte, comme indiqué sur la première photo.
Maintenant, vous devez endommager la piste, comme sur la deuxième photo et changer les fils dans le bloc, comme sur la troisième photo.
Septième étape: installation du moteur, de la poulie, de la courroie
Installe le moteur. Sur l'arbre, le moteur fixe une poulie. La deuxième poulie se place du côté opposé du moteur. Attache l'extrémité de la ceinture avec des liens. Passe la deuxième extrémité de la courroie à travers les poulies et se fixe également.
Étape huit: Fondation
La base est en contreplaqué. Pour lui, le maître attache l'axe X.
Étape neuf: axe Y
Collecte l'axe Y. C'est une étape difficile.
Assemblez le support de poulie à l'aide du support de poulie de l'axe Y, de la poulie, du boulon / écrou M4 de 40 mm et des rondelles métalliques, comme indiqué sur les deux premières photos.
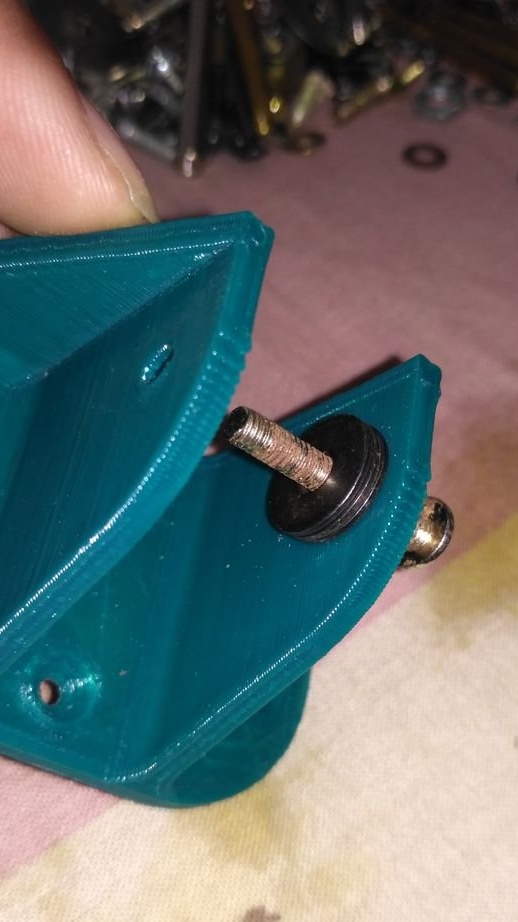
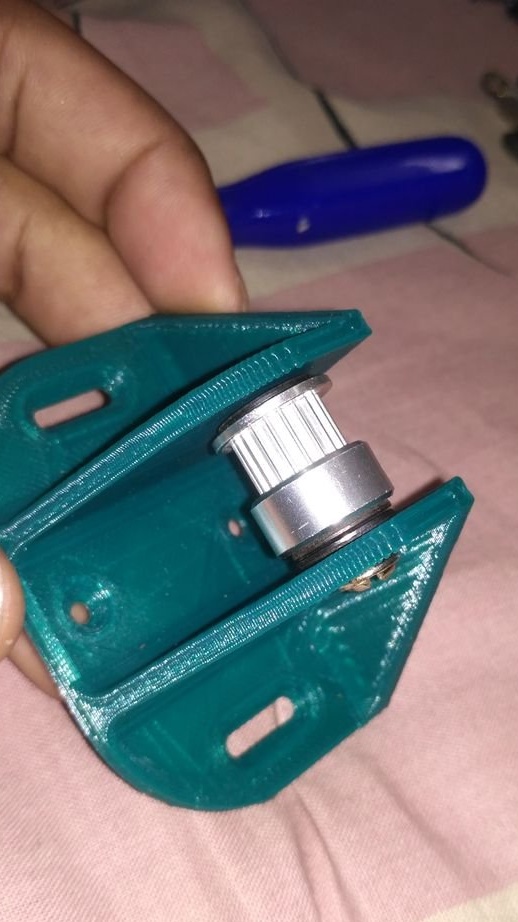
Attachez maintenant une extrémité de la courroie de distribution à l'une des fentes sous le chariot de l'axe Y.
Passez l'extrémité libre de la courroie à travers l'ensemble de poulie que vous avez fait précédemment, puis enclenchez-la dans la deuxième rainure située sous le chariot de l'axe Y.
Une fois ces 3 étapes terminées, vous devez visser l'assemblage de l'axe Y à la base en contreplaqué.
Fixez le moteur pas à pas au support de moteur de l'axe Y à l'aide de deux boulons et écrous M3 de 12 mm.
Vissez maintenant le support de poulie de l'axe Y et le support moteur à la base en contreplaqué.Pour ce faire, après avoir réglé les deux côtés pour obtenir la tension de courroie correcte. Un tendeur de courroie sera ajouté ultérieurement.
Étape dix: Module laser
Comme indiqué, dans le cahier des charges, la machine a mis en place un remplacement rapide du module laser par d'autres modules exécutifs. Pour cela, le maître a réalisé deux pièces rectangulaires (couvertures). Six aimants en néodyme sont installés dans chacun. Un couvercle est attaché à l'axe X, le module laser est attaché à l'autre.
Les fils sont montés comme suit.
Les lasers + et - sont connectés respectivement à V + et V- du module MOSFET. L'alimentation est connectée à VCC et GND respectivement. Le fil de signal est connecté à la broche de signal du module MOSFET.
Étape onze: traceur
Collecte un traceur. Dès que les deux parties sont imprimées, le maître polit les plans qui sont en contact les uns avec les autres, les lisse avec une lime et du papier de verre, jusqu'à ce que les deux parties glissent ensemble avec très peu de frottement.
Serrez maintenant les vis M3 de 40 mm et réglez le ressort.
Le servomoteur, les bornes et les bâtons Arduino comme indiqué sur la photo.
Ici Arduino nano est utilisé pour convertir les signaux de contrôle laser en signaux PWM pouvant entraîner un micromoteur.
Il est connecté comme suit:
+5 Volt - Vin
-5 Volt - GND
Signal - D10
Puissance servo + ve - 5V
Servo power -ve - GND
Signal servo - D3
Ensuite, le code est chargé.
#include Servo myservo;
void setup ()
{
myservo.attach (3);
pinMode [10, ENTRÉE];
}
boucle vide ()
{
if (digitalRead (10) == HIGH)
{
myservo.write (20);
}
d'autre
{
myservo.write (60);
}
}
Étape douze: Installation
Installation selon le schéma.
Le convertisseur boost est réglé sur 12V.
Arduino est installé dans le module d'extension CNC.
Le ventilateur est collé au trou prévu à cet effet avec un adhésif thermofusible.
Une bande LED a été ajoutée pour l'apparence et l'indication de puissance.
Le boîtier imprimé est vissé au contreplaqué.
Une feuille acrylique transparente de 87 x 75 mm 2 mm d'épaisseur est utilisée comme revêtement de corps. Il peut être inséré à travers la rainure prévue à cet effet sur un côté du boîtier.
Les fins de course sont fixés de manière à ce que le bouton soit enfoncé de 3 mm avant que les roulements de chaque chariot entrent en collision avec les supports de traction.
Les fils des moteurs et des interrupteurs de fin de course sont allongés et les connexions sont isolées.
Les fils sont collés à la base en contreplaqué avec de la super-colle.
Ici, le convertisseur boost est utilisé uniquement pour alimenter les puces du pilote de moteur A4988. Chaque moteur ne consomme que 150 mA de courant.
Étape 13: Module Bluetooth
Monte le module Bluetooth.
Pour envoyer et recevoir des données ou, dans ce cas, des codes G via le module Bluetooth HC05, vous devez d'abord configurer le module.
Connectez le module HC05 à l'Arduino Uno, comme illustré dans la première figure.
Téléchargez le code attaché à cette étape sur Arduino.
BLUE_P.ino
Saisissez maintenant les codes indiqués sur la deuxième photo.
Après avoir terminé les réglages, déconnectez le module HC05 de l'Arduino que vous avez utilisé pour la programmation et connectez-vous au blindage CNC Arduino conformément au schéma de circuit de la 3ème photo.
Étape quatorze: code et configuration
Pour un graveur laser, le maître télécharge le code.
GRBL.zip
Laser GRBL est l'un des meilleurs streamers de code G gratuits pour les graveurs laser. Il peut directement transférer des codes G vers Arduino via le port som. Il dispose d'un outil intégré pour convertir les images en codes G.
Tous les réglages doivent être effectués comme sur la photo, en tenant compte des éléments suivants:
Installez le port silure auquel votre graveur laser est connecté.
Les valeurs de configuration peuvent être modifiées en fonction de votre graveur.
Étape 15: Test
Une fois le laser connecté, il est temps de vérifier sa précision.
Il y a quelques points à vérifier:
Les axes X et Y se déplacent-ils dans la bonne direction?
Le référencement fonctionne-t-il correctement?
Le moteur saute-t-il des étapes en raison d'un frottement élevé ou de courroies trop tendues?
Les tailles des images imprimées correspondent-elles aux tailles indiquées dans le logiciel? Le nombre de pas par mm correspond-il au moteur pas à pas utilisé?
La tension de la courroie peut être réglée à l'aide du tendeur. Tournez le boulon jusqu'à ce que la tension correcte soit atteinte.
Pour vérifier si le moteur a des étapes et les dimensions correctes, affichez une simple figure géométrique continue, par exemple, un carré, un triangle ou un cercle. Si le laser démarre à partir d'un point et s'arrête idéalement au même point, cela signifie que votre laser n'a pas manqué une seule étape et fonctionne parfaitement. Une fois le triangle ou le carré imprimé, mesurez manuellement sa taille avec une règle et voyez s'il correspond aux dimensions que vous avez spécifiées.
Selon le capitaine, il est entièrement satisfait de la machine.
Peut être gravé sur divers matériaux tels que le bois, le carton, le cuir, le plastique, etc.
Le moteur ayant environ 102 pas par mm, de minuscules gravures aux détails fins peuvent être réalisées.
Le graveur a travaillé sans problème sur l'alimentation USB.